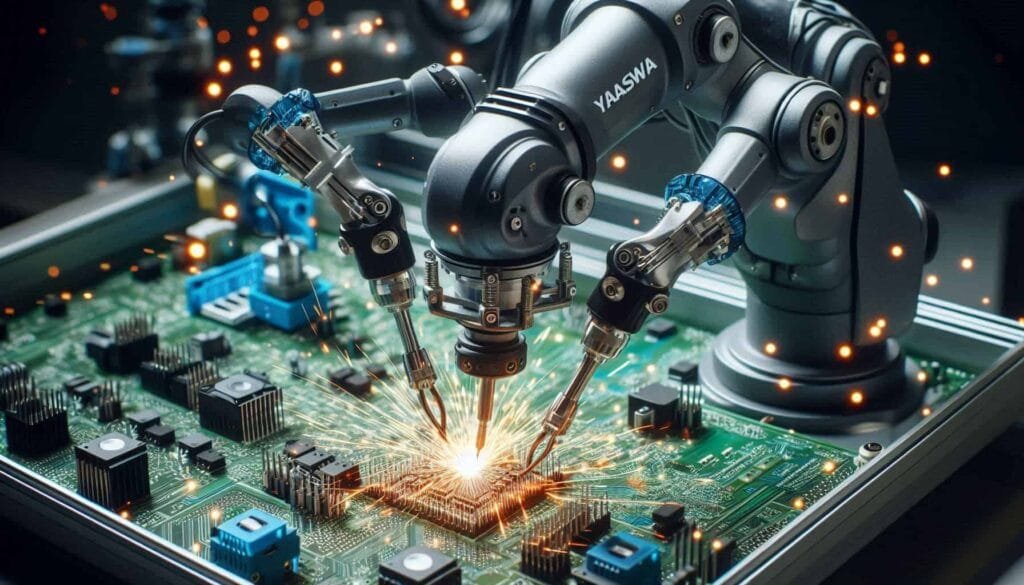
Robotics and automation keep transforming sectors, allowing more flexible, exact manufacturing lines by means of their efficiency. Programmable Logic Controllers (PLCs) together with Yaskawa robot arms offer the perfect solution for this change. This article will walk over how to trigger yaskawa robot arm trough plc and explain the required actions to reach a flawless integration.
Overview of Yaskawa Robot Arms and PLCs
Leading robotic systems in their field, Yaskawa robot arms provide remarkable performance for jobs including material handling, welding, and assembly. Industrial automation favors these robots since they are quite appreciated for their accuracy, dependability, and adaptability.
Programmable Logic Controllers, or PLCs, are specifically designed computers used in industrial automation. Modern automated systems depend on them since they can manage difficult procedures and operate machines.
Combining a PLC with a Yaskawa robot guarantees flawless control and synchronisation, therefore creating a variety of opportunities to increase industrial automation and efficiency.
Understanding the Basics
What is a Yaskawa Robot Arm?
Designed for a great range of industrial uses, a Yaskawa robot arm is a highly adaptable, programmable robotic device. Robust construction and great accuracy in jobs including welding, painting, packaging, and assembly define these robots.
What is a PLC (Programmable Logic Controller)?
A PLC is a digital computer applied for industrial system control and automation. It tracks inputs from many sensors, runs them in line with pre-programmed logic, and generates outputs to robots, machines, and actuators. It is extensively applied in sectors including electronics, food processing, and automobile control of industrial processes.
Benefits of Triggering a Yaskawa Robot with a PLC
Enhanced Automation
Complex industrial chores can be automated by running a how to trigger yaskawa robot arm trough plc. Higher throughput and less human involvement resulting from this help to increase operational efficiency.
Increased Precision and Flexibility
Using a PLC enables more exact and adjustable control of the robot arm, therefore enabling fine-tuned actions depending on particular needs. The adaptability to various production needs is guaranteed by the freedom to reprogram activities.
Streamlined Industrial Processes
Integration lessens the requirement for several systems’ independent controllers. By managing robot arms, conveyors, and other gear one PLC can help to create a more coherent manufacturing line.
Key Components Required
Integration of a Yaskawa robot with a PLC calls for the following components:
- Yaskawa Robot Arm: The robotic mechanism in charge of completing particular duties.
- PLC Hardware and Software: a controller and the related program to regulate the logic of the system.
- Communication Protocols: Protocols guaranteeing flawless connection between the robot arm and the PLC include Ethernet/IP or Profinet.
- Programming Environment: Programming the PLC and the robot uses different software tools.
Communication Protocols Overview
Importance of Communication Protocols
Reliable data moving between the PLC and the Yaskawa robot depends on communication protocols. These systems guarantee seamless integration by controlling data format, transmission, and processing across the system.
Types of Protocols Supported by Yaskawa Robots
Usually supporting several communication systems, yaskawa robots consist:
- Ethernet/IP: a frequently used industrial protocol for Ethernet-based communication.
- Profinet: a rapid communication protocol grounded on Ethernet for industrial automation systems.
- DeviceNet: Frequently used to link PLCs, actuators, and sensors—among other automation parts.
Setting Up the System
Hardware Connections
Establish first the physical link between the PLC and the Yaskawa robot controller. Usually, this entails matching Ethernet cables or other communication hardware to the corresponding ports on both devices.
Connecting the PLC to the Yaskawa Controller
Make sure the suitable communication interface—Ethernet/IP, Profinet, etc.—connects the PLC to the controller of the robot. The robot controller should be able to get and evaluate PLC commands.
Software Preparation
Install the required PLC and robot software prior to integration. For the PLC, this covers the logic programming tools; for the robot, the Yaskawa programming environment.
Configuring the Robot Controller
Get the controller software for the robot and set it to take PLC commands. Setting up communication parameters including IP addresses and port numbers helps to guarantee that the devices may interact successfully.
Configuring the Yaskawa Robot Controller
Steps to Set Communication Parameters
- Open the configuring interface of the robot.
- Now enter the proper network settings—IP address, subnet mask, etc.?
- Set the communication protocol parameters in line with PLC capability.
Synchronizing Robot Controller with the PLC
Set the communication parameters then synchronise the robot controller with the PLC to enable real-time transmission between the two systems.
Programming the PLC for Robot Triggering
Writing the Basic PLC Logic
Write the fundamental PLC logic first for robot arm control. This will entail designing procedures based on input criteria that transmit trigger signals.
Assigning I/O Points for Robot Triggering
On the PLC, set aside particular I/O points to match robotic triggers. A particular input signal might tell the robot, for instance, to begin a job involving object placement or picking.
Creating Robot Jobs on Yaskawa Controller
Specify the duties (tasks) the Yaskawa robot controller will carry out upon PLC prompted activation. This covers clearly the precise motions and acts required for the employment.
Integrating PLC and Robot
Linking Robot Jobs to PLC Instructions
Connect the jobs of the programmed robot to related PLC commands. This guarantees that the robot carries out the suitable action when the PLC sets a certain signal trigger.
Example of a Trigger-Based Workflow
A trigger-based workflow might have the PLC identifying a particular situation, say the completion of a prior task. Once this condition is satisfied, the PLC triggers the robot to start the next job in the process.
Testing and Debugging
Verifying Connections
Check that every hardware connection is operating as it should once everything is linked and coded. Verify that the robot controller and the PLC can communicate.
Testing Trigger Signals
Verify that the PLC’s trigger signals correctly start the motions of the robot. Running little test cycles to guarantee seamless operation could be part of this.
Troubleshooting Common Errors
Deal with frequent problems such defective wiring or improper communication settings that could compromise the integration. Troubleshooting in the PLC and robot programming environments uses the diagnostic instruments.
Applications of PLC-Triggered Robots
Manufacturing and Assembly
Commonly seen in assembly lines, PLC-triggered robots can complete repeated operations such sorting, packaging, or item assembly.
Material Handling
Material handling jobs such carrying goods from one place to another or stacking goods in warehouses can be handled by robots.
Welding and Painting
Where great consistency and accuracy are needed, PLC-triggered Yaskawa robots are also employed for painting and precise welding.
Best Practices for PLC and Yaskawa Integration
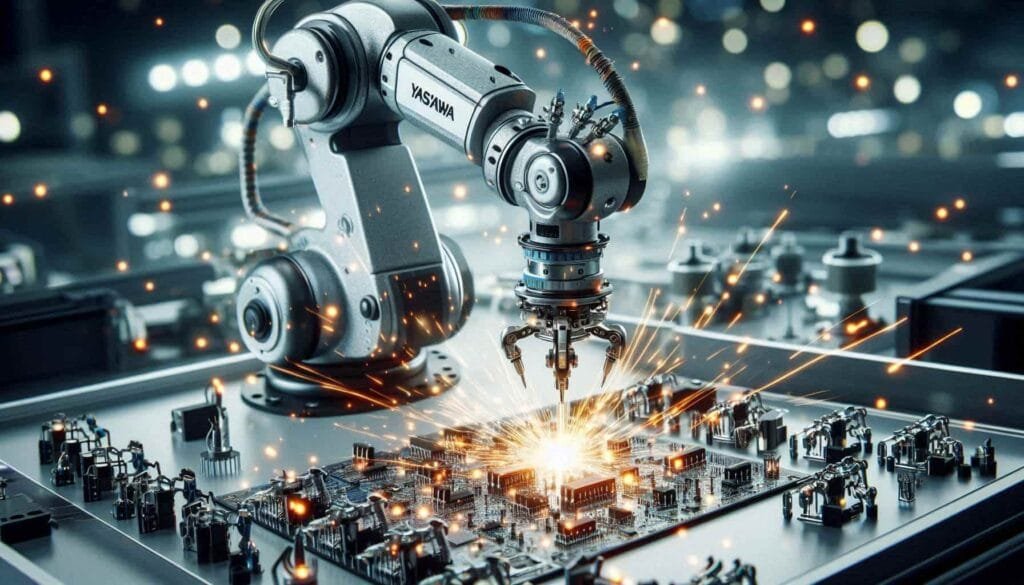
Ensuring Safety
Always make sure that protective barriers to stop mishaps and emergency stop systems are followed.
Regular Maintenance of Components
Maintaining optimal condition and continuous operation of the PLC and robot depend on regular maintenance, hence.
Optimizing Communication Settings
By means of optimal communication parameters like network speed and signal integrity, one may guarantee dependable and smooth operation of the integrated system.
Challenges and Solutions
Connectivity Issues
Particularly with sophisticated network configurations, PLC and robot connectivity problems can arise. Correcting network congestion and guaranteeing appropriate wiring help to minimise these issues.
Timing Mismatches
Errors or delays might arise from timing mismatches between the PLC signals and the robot’s operation. One can help to remedy this by adjusting the time parameters and applying buffer zones.
Addressing Software Bugs
Regular software debugging and updating guarantees that PLC or robot control software faults are found and corrected fast.
Conclusion
Combining a PLC with a Yaskawa robot arm creates many ways to improve industrial automation. Following the correct procedures for hardware connection, software configuration, and programming will help manufacturers create very flexible, precise robotic systems. Further developments in robotic automation are envisaged as technology develops, so enhancing the power and adaptability of these systems.
FAQs
1. What types of PLCs work best with Yaskawa robots?
Supported standard industrial protocols such Ethernet/IP, Profinet, or DeviceNet, the finest PLCs for Yaskawa robots are those ones.
2. Can a single PLC control multiple Yaskawa robots?
Indeed, if a single PLC is programmed properly and set with the required communication channels, it may manage several robots.
3. How long does it take to set up a PLC-robot integration?
The intricacy of the system determines the setup time; but, a complete integration usually takes a few hours to many days.
4. What safety measures should be implemented?
To prevent mishaps, safety precautions should call for emergency stops, safety sensors, and operator adequate training.
5. Is specialized training required for programming?
Indeed, to guarantee effective and error-free operation of the PLC and the robot controller, specialised training is usually necessary.